Сучасна система управління виробництвом: повномасштабна цифровізація виробничих майданчиків «Стальканат» у концепції Industry 4.0
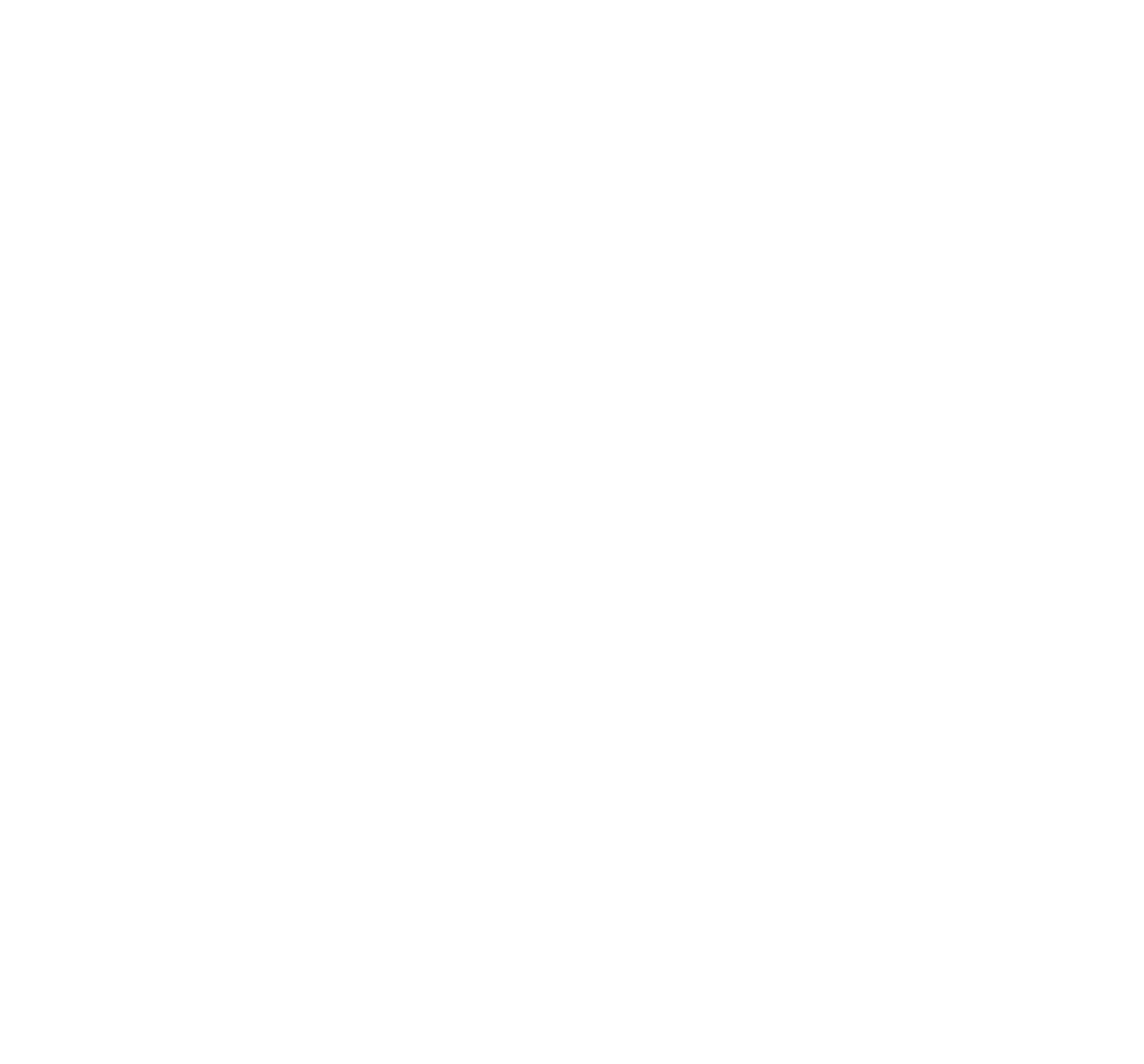
масштаб | 1200 співробітників | kpi | Оптимізація бізнес-процесів |
---|---|---|---|
Продукт | Виробництво | Тривалість проекту | 12 місяців |
Рік кейсу | 2023 | Країна | Україна |
Галузь | Кабельно-дротова, металовиробнича промисловість | Замовник | Стальканат, СДКВ |
Компанія «Стальканат», один із найбільших виробників сталевих канатів та арматурних пасм у Східній Європі, лідер виробництва метизної продукції в Україні. Підприємство має асортимент з понад 6000 маркорозмірів дроту та понад 1500 маркорозмірів канатів.
Передумови проєкту
Рушійною силою, яка змусила розпочати процес побудови сучасної системи управління виробництвом, став рух компанії на закордонні ринки.
Інформаційна інфраструктура компанії до старту проєкту з впровадження єдиної комплексної системи на no/low-code платформі IT-Enterprise нараховувала багато різнорідних, не зв'язаних між собою програмних продуктів (Excel, 1С, системи управління виробництвом власної розробки тощо). Подібний підхід не дозволяв наскрізно й ефективно керувати бізнес-процесами підприємства і гальмував розвиток компанії.
Перед початком проєкту цифрової трансформації підприємство ставило перед собою цілі з підвищення прозорості функцій і бізнес-процесів, побудови наскрізних процесів управління та покращення KPI бізнесу.
Цифровізація виробництва «Стальканат» почалася з Цеху сталевого дроту (ЦСД) та завершилася цифровізацією двох майданчиків Сталедротового канатного цеху (СДКЦ), розгорнутий опис проєкту додається нижче.
Етапи проєкту
Комплексний проєкт з побудови сучасної системи управління виробництвом у системі IT-Enterprise являє собою послідовний ланцюг підпроєктів з наступних напрямків:
MDM — управління основними даними
Побудова MDM (Master Data Management — управління основними даними) єдиної моделі даних супроводжувалася розробкою єдиної бази всіх класифікаторів, довідників підрозділів та інших нормативних довідників.
Важливим завданням MDM є забезпечення єдності класифікації, кодування, іменування однорідних об'єктів (матеріально-технічних ресурсів, контрагентів, послуг тощо). Таке поєднання знімає безліч проблем, що виникають через невідповідність і непорівнянність даних, знижує трудомісткість формування звітності, усуває дублювання.
MDM дозволяє об'єднати, уніфікувати і синхронізувати всі основні дані та створити на підприємстві єдину цифрову екосистему.
WireDesigner — полегшує введення нормативної бази (за оцінками на 80%)
Підпроєкт з цифровізації процесів розробки нормативно-довідкової інформації (НДІ) і технологічної підготовки виробництва (ТПВ) охоплював запуск системи автоматизованого проєктування технолога (САПР-Т), за допомогою якого розробляються норми та технологічні процеси для нових виробів.
Фактично WireDesigner — це унікальний інструмент, який пришвидшує введення нормативної бази на 80%. Завдяки цьому інструменту підприємство швидко — за 6 місяців — підготувало нормативну інформацію та перейшло до завдань цифровізації управління виробництвом на пілотному майданчику (ЦСД).
Підприємства з виробництва метизної продукції та канатів мають широку номенклатуру продукції, яка може нараховувати сотні тисяч маркорозмірів. Лінійка є настільки широкою, що введення НДІ може зайняти місяці або навіть роки у випадку якщо це зробити без допоміжних інструментів.
Тож WireDesigner покликано вести єдину базу НДІ та ТПВ для поточної продукції і значно прискорює подальші процеси вводу нормативної бази для нових виробів.
Оцінка термінів обіцянки із використанням сучасних методів календарного планування: MPS, MRP, APS
Традиційний спосіб встановлення термінів обіцянки виконання замовлень, за відсутності спеціальних інструментів, спирається на розуміння часу технологічного циклу виробництва кожної групи продуктів. До якого механічно додається ще і запас часу термінів обіцянки (тимчасові рамки): +2 тижні або при дискретному наборі — перенесення на першу/другу половини наступного місяця.
IT-Enterprise пропонує два концептуальних підходи для вирішення завдання з оцінки термінів обіцянки.
- Перший підхід: при впровадженні інструментів календарного планування, як-от: MPS, MRP, APS, процес може виглядати наступним чином:
1 служба збуту приймає замовлення, бере паузу у 1 день і передає замовлення до служби планування виробництва → 2 служба планування виробництвом додає замовлення до загального портфеля, планує їх разом і отримує доволі точні терміни обіцянки → 3 служба збуту повертає клієнту інформацію про терміни обіцянки виконання замовлення → 4 клієнт погоджує прораховані терміни обіцянки і замовлення передається у виконання.
Інструменти календарного, оптимізаційного планування пов'язані між собою і на їхній підставі виконується оцінка термінів обіцянки, серед них:
> MPS (Master Production Schedule — головний календарний план виробництва);
> MRP (Manufacturing Resource Planning — планування ресурсів виробництва);
> APS (Advanced Planning & Scheduling — оперативне планування виробництва).
- Другий підхід: при впровадженні інструментів об'ємно-календарне планування виробництва, як-от CRP (Capacity Requirements Planning — планування виробничих потужностей) оцінка термінів обіцянки є більш грубою, але швидшою.
Управління виробництвом: MPS, MRP, APS, MES
За стратегією побудови системи управління виробництвом було прийнято рішення стандартизувати бізнес-процеси згідно MPS, MRP, APS, MES, що перетворило випуск кожного замовлення на підприємстві на чіткий та послідовний процес з розписаними технологічними операціями:
- Технолог, за допомогою інструмента WireDesigner, розробляє нормативно-довідкову інформацію (НДІ) під маркорозмір і виробництво кожного замовлення розраховується за технологічним ланцюжком. Фактично до кожного замовленням додається план його виробництва.
- Далі всі замовлення групуються між собою за APS-правилами планування та розкладаються по обладнанню в цеху.
- На основі плану виробництва формуються електронні змінні завдання.
Спочатку планувальник будує оптимальний виробничий план, далі, за допомогою змінних завдань, доводить до цеху інформацію у вигляді змінних завдань.
Цех на мобільні пристрої отримує електронні змінні завдання за етапністю виробництва. Своєю чергою виконавці за допомогою MES (Manufacturing Execution System — система управління виробництвом) фіксують факт виробництва електронно і цим дають зворотний зв'язок планувальнику. Кросвзаємодія підрозділів відбувається через мобільний застосунок, фактом закриття змінних завдань і реєстрації факту виконання. - У плані закриваються позиції фактом виконання змінного завдання.
- Далі планувальник перераховує оперативний план виконання і бачить як, з урахуванням факту виробництва, змінилися терміни випуску (скоротилися або додалися) стосовно терміну обіцянки, який зафіксовано в момент прийняття замовлення в роботу.
Використання детальних планів та електронних змінних завдань у розрізі замовлення, дозволяє простежувати виконання кожного з них. А також на підставі точних даних дозволяє швидко планувати, здійснювати та контролювати оперативні коригування при управлінні виробництвом, максимально усуваючи людський фактор і не витрачаючи зусилля на ручний контроль — система відображає поточний стан онлайн.
Керованість процесу значно підвищується, а витрати годин на процеси управління і контролю зменшується. Персонал має час спрямувати свою увагу на інші нагальні питання, як-от: дотримання технологічних процесів, стандартів, якості, оптимізацію виробництва.
Організація оперативного позамовного обліку незавершеного виробництва (НЗВ) у цеху без зупинок на інвентаризаційні зміни
На підприємстві впроваджено відстежування послідовності процесів:
1 на підставі електронних змінних завдань реєструється виробництво кожної технологічної партії (барабан, котушка, бунт) → 2 кожна технологічна партія маркується ярликом відразу в момент виробництва → 3 технологічна партія через ярлик збагачується інформацією про всі деталі замовлення і виробництва → 4 в момент передачі партії на наступну технічну операцію обробки фіксується її вхід на виконання.
Тож побудовано зв'язок і наступність процесів: реєструється відмітка часу виробництва замовлення та інформація щодо стану напівфабрикатів, якщо це перша технічна операція — то реєструється партія матеріалу.
У процесі виробництва фіксується повний матеріальний потік (від приходу сировини до випуску готової продукції). Дані по баланс матеріалів та напівфабрикатів кожного виробничого підрозділу змінюються онлайн і доступні 24/7 для всіх учасників виробничих та інших процесів.
«Раніше підприємство зупинялося для проведення інвентаризації мінімум на одну зміну. Відтепер підприємство працює без щомісячної зупинки виробництва. Адже завдяки системі IT-Enterprise наявність і статус партій доступні в режимі реального часу.
У «Стальканат» з'явилося додатково +12 змін роботи заводу на рік, а це додаткові тони випуску продукції. Тільки ці показники спроможні окупити весь проєкт за 3-4 роки максимум. На мою думку, це є найголовніший кейс цифровізації», — коментує, фінансовий директор «Стальканат».
Цех працює лише за змінними завданнями, які формуються на основі виробничого плану. Змінні завдання робляться виключно під план випуску, а план випуску містить лише перелік замовлень від клієнтів.
«Система IT-Enterprise робить “помітними” “ходові” НЗП. Як результат — у Цеху сталевого дроту скорочено “неходові” НЗП на 50-60%, прямий фінансовий ефект склав приблизно 28 тис. євро на рік. Це дозволило керовано збільшити “ходові” НЗП на значно більшу суму.
Відтепер менеджмент підприємства свідомо приймає рішення щодо дій з НЗП, розуміючи точну кількість залишків в режимі реального часу. Раніше актуалізація інформації займала до 5 днів і потребувала завантаження роботи п'ятьох IT-фахівців.
По моїй експертній оцінці подібні дії генерують прибуток через скорочення простоїв і зростання виробництва в місяць на 5%, що становить значні грошові суми», — коментує фінансовий директор «Стальканат».
Зниження НЗВ призвело до економії на банківських кредитах і виключило заморожування оборотних активів до 30 тис. євро щорічно.
Управління якістю: вхідний контроль, поопераційний контроль, приймально-здавальні випробування
На підприємстві налаштовано процес повного контролю якості (SmartQuality): починаючи від вхідного контролю сировини та матеріалів до приймально-здавальних випробувань.
Відбуваються сотні випробувань на день, сотні тисяч на місяць: кожен бунт дроту, який знімається зі стану проходить випробування практично після кожного переділу. Завдяки чому брак можна відстежити на кожній стадії процесу. Дані випробувань впливають на якість заготівлі чи готової продукції та є індикатором відповідності вимог клієнта.
Наразі після кожної операції перероблення напівфабрикатів виконується контроль. Система автоматизовано контролює результати міжопераційного контролю та виключає людський чинник. Також це дозволяє накопичувати статистику, яка потім перетворюється на більше ефективні рішення з управління виробництвом.
Електронний торговий майданчик SmartTender для забезпечення логістики
Підприємство оптимізувало логістичні операції через розміщення заявок на перевезення через електронний торговий майданчик SmartTender.
«У перший рік використання подібного підходу підприємство заощадило близько 1 млн грн на логістиці, тим самим збільшивши маржинальність замовлень на цю суму. Щорічно цифра зростає пропорційно зростанню обсягів», — коментує фінансовий директор «Стальканат».
Управління складами металевої катанки
Підприємство побудувало процеси планування надходження, розміщення, контролю та видачі сировини у системі управління складом (WMS, Warehouse Management System). Кожен бунт катанки промарковано, що дозволяє ідентифікувати її знаходження на складському майданчику та спростити складську логістику всередині підприємства.
Спростився і процес забору катанки: комірник бачить переміщення в системі та складський баланс, контроль залишків відбувається за допомогою терміналу збору даних (ТЗД-сканер) через сканування бунтів, що знаходяться на складі.
Масштабування системи управління виробництвом «Стальканат» почалося з Цеху сталевого дроту (ЦСД), який виробляє арматурні пасма, фібру, зварювальні та пружинні дроти, та завершилося цифровізацією бізнес-процесів Сталедротового канатного цеху (СДКЦ), який виробляє канати та дріт із різними видами гальванічного покриття.
Фактично три великих фабрики пройшли процес цифрової трансформації. Впровадження першого проєкту відбувалося швидко, із максимальним залученням команди IT-Enterprise, два наступні проєкти — впроваджувалися самостійно силами власного Центра компетенції (ЦК).
ЦК був створено замовником з самого початку співпраці «Стальканат» і IT-Enterprise, команда пройшла практику впровадження цифрових інструментів на першому об'ємному проєкту.
Розгортання цифровізації на нових виробничих майданчиках СДКЦ силами власного центру компетенцій значно знизило витрати підприємства на впровадження і підтримку IT-системи.
Технології Industry 4.0
У проєкті цифровізації використовувалися сучасні методи управління виробництвом, як-от:
> оптимізаційне планування виробництва APS із застосуванням теорії обмежень для оптимального завантаження виробництва та планування термінів випуску замовлень;
> інструмент WireDesigner для пришвидшення введення нормативної бази;
> WMS, MES з використанням мобільних пристроїв для переходу на мобільний, в реальному режимі часу, облік сировини, напівфабрикатів і готової продукції на складах та у виробництві.
Ключові показники
Наведено кілька прикладів ефективностей, які вдалося досягти в результаті виконання проєкту цифровізації системи управління виробництвом підприємства «Стальканат»:
Описаний вище проєкт побудови системи управління виробництвом «Стальканат» є частиною цифровізації підприємства. Подальший розвиток триває, зараз відбувається впровадження фінансового проєкту з оптимізації процесів збуту, закупівель, казначейства, бюджетування та бухгалтерії.
«Стальканат» вийшов на завдання оптимізації виробничого плану за допомогою штучного інтелекту (ШІ), що дозволить у періоди підвищеного попиту максимізувати випуск і задовольнити більшу кількість запитів клієнтів.
Відеокейс з roadmap впровадження Industry 4.0 й отримання ефекту у «Стальканат», Цех сталевого дроту (ЦСД), за посиланням. А також кейси:
> перехід ремонтної служби на роботу з мобільним застосунком SmartEAM щодо реактивного обслуговування за заявками на ремонт, за посиланням
> трансформація виробництва за принципами Industry 4.0, з оптимізації кожного етапу виготовлення продукції, за посиланням
> реінжиніринг бізнес-процесів у концепції Industry 4.0 що здійснювався поетапно та за допомогою програмних бізнес-рішень, які є частинами SmartFactory, за посиланням