ОЛЕНА АБАШЕВА (ЕФЕКТИВНЕ УПРАВЛІННЯ ВИРОБНИЦТВОМ: ЯК ВИРІШИТИ НАЙБІЛЬШ АКТУАЛЬНІ ПРОБЛЕМИ НА МАШИНОБУДІВНИХ ПІДПРИЄМСТВАХ?)
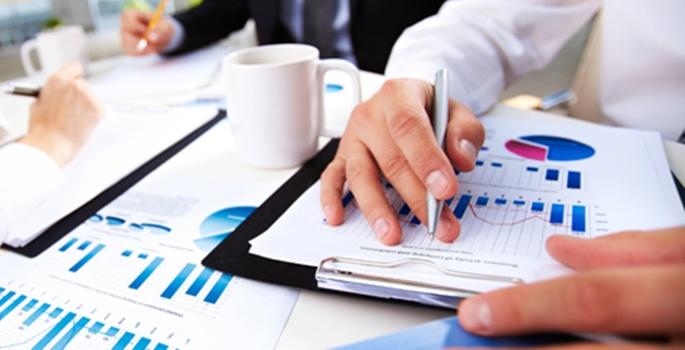
Джерело: Портал машинобудування
Автор: Олена Абашева
Звітний відеоролик про роботу Машинобудівного форуму 2012
Відео виступу учасників Форуму
Машинобудівний форум "Ефективне управління машинобудівним виробництвом– кращі практики" відбувся в Одесі с 24 по 25 квітня. На Форумі учасники змогли поділитися досвідом впровадження та обговорити такі актуальні питання, як: з чого розпочати машинобудівному підприємству — якими повинні бути перші кроки по впровадженню ERP-системи? Як правильно зазначити цілі по проекту впровадження? Як бути, якщо технології не встигають описати необхідні технічні процеси ? Як керувати собівартістю? Представляємо публікацію Порталу машинобудування по підсумкам Форуму.
Машинобудівний форум – чому та навіщо?
Кожне машинобудівне підприємство часто вирішує проблеми по своєму та по новому "винаходить велосипед", не дивлячись на наявність досвіду по вирішенню існуючих проблем в СНД та світі. І, "як повітря", потрібен майданчик для того, щоб можливо було озвучити цей досвід, обсудити найбільш важливі проблеми та знайти їх рішення.
З цією метою і був створений Машинобудівний форум "Ефективне управління машинобудівним виробництвом – кращі практики", який відбувся з 24 по 25 квітня в Одесі.
Організатором Форуму виступила Корпорація "Інформаційні технології" (Україна). Компанія є розробником корпоративної системи управління IT-Enterprise – ERP, MRP II, MES, APS, EAM-системи, орієнтованої на комплексну автоматизацію промислових підприємств.
Обмінятися досвідом учасники змогли на пленарних засіданнях та у рамках "круглих столів". Демонстрація можливостей системи та проговорення загальних проблем пройшли на спеціально організованих майданчиках по управлінню інженерної підготовки виробництва, управлінню виробництвом, управлінню собівартістю та затратами.
Загальну ситуацію на машинобудівних підприємствах та особливості впровадження проектів представили генеральний директор корпорації "Інформаційні технології" Олег Щербатенко та технічний директор Володимир Михайлов.
Машинобудівні підприємства: проблеми і тенденції 2000-х рр.
У своєму виступу Олег Щербатенко, генеральний директор корпорації "Інформаційні технології", виділив загальні проблеми підприємств машино будівництва:
- Перехід від серійного виробництва до випуску на замовлення унікальної продукції.
- Посилення вимог до скорочення терміну випуску; зменшення часу циклів підготовки виробництва та самого виробництва.
- Необхідність в оптимізації управління виробництвом, завантаження потужностей, контролю витрат, визначення собівартості без вартості виробів.
- Підйом пропускної здатності виробництва.
Володимир Михайлов, технічний директор Корпорації "Інформаційні технології", відмітив наступні важливі тенденції 2000-х–2010-х рр. для машинобудівних підприємств:
- Фактично всі підприємства стали мілко серійними та одиничними, виготовляють "персоналізуються вироби/серії".
- Відбувається різке розширення кількості модифікацій виробів, продуктової лінійки і, як наслідок, "вал" зміна КТД.
- Створюються машинобудівні холдинги, іде централізація управління заводами. Частина функцій управління виноситься до холдингу.
- Підвищується вартість залучення позикових коштів.
- Залучення кваліфікованого персоналу робити стає складніше.
Конкуренція на ринку посилюється, і боротьба за Замовника іде по всім направленням: термінам поставки продукції, можливості забезпечити своєчасне відвантаження замовлень, лояльною ціною та високою якістю продукції, виконанню договірної дисципліни.
Перехід до більш ефективного управління виробництвом підприємства виконують за допомогою реінжинірингу бізнес-процесів та впровадженню ERP-системи.
Хто ініціює проект і навіщо?
Ініціація проекту "оптимізації виробничого планування та обліку" виходить від таких осіб та підрозділів підприємств :1. Від власника/генерального директора/керуючої компанії
2. Від комерційної служби – навіщо?:
- Забезпечити потребу пропускної здатності виробництва.
- Скоротити термін відклику на запит клієнта.
- Довести коефіцієнт обслуговування до 90% та вище, т. я. відвантажувати замовлення у погоджені з Замовником терміни.
3. Від фінансово-економічної служби – навіщо?:
- Забезпечити фінансовій результат діяльності.
- Обійтись заданим об’ємом абстрактними активами (фінанси, можливості, люди, матеріали…)
- Забезпечити задану рентабельність.
4. Від виробників – навіщо?:
- Виконати план своєчасно при багатьох заборонах.
"Перемагає не сильний, Перемагає швидкий" , або які результати оптимізації управління виробництвом?
Результатами проектів по оптимізації виробничих процесів стають:
- Підйом рівня обслуговування та випуск замовлень в термін.
- Підйом пропускної здатності заводу при одночасному зниженні численності персоналу.
- Скорочення фактичних циклів виробництва/проектування.
- Скорочення об’ємів абстрактних активів (запасів готово продукції, НЗП та складських запасів).
- Виконання оперативного контролю витрат на виробництво та прогноз фінансового результату.
- Виробництво стає прозорим для управління — в результаті піднімається швидкість прийняття рішення — « Перемагає не сильний, Перемагає швидкий»
ПРИКЛАД
ДП НПКГ "Зоря"-"Маш проект": одне з найбільших машинобудівних підприємств України (12 тис. працюючих).
Комплексна інформаційна система (КІС) на платформі ERP-системи IT-Enterprise експлуатується більш ніж 10 років.
Загальна кількість користувачів системи – більш ніж 2600.
Середня кількість одночасно працюючих користувачів – 1500.
Об’єм бази даних КІС – більше ніж 500 Гб.
Перед системою управління ставились завдання:
- Підтримка росту виробництва в натуральному та вартісному виразі.
- Виявлення та впровадження рішень, направлених на зниження витрат та підвищення продуктивності праці.
Основний результат — підприємство постійно підвищує об’єм випуску на 20-30% на рік.
Всі дії конструкторів, технологів, економістів, плановиків, постачальників та іншого персоналу по "просуванню" виробів від проектування креслення та планування виготовлення до постачання, виготовлення у цехах та відправки виробу замовнику – "диригують" системою.
Основний ефект досягнуто від зниження матеріальних запасів та об’єму незавершеного виробництва, скорочення виробничого циклу, контролю фінансового бюджету та скорочення штрафних санкцій зі сторони контролюючих органів, контролю за нормуванням матеріальних та трудових ресурсів, контролю міжзаводської кооперації.
"Всі цеха раніше ходили в службу забезпечення та підписували документи на отримання матеріалів зі складу. В такому русі знаходилось принаймі 400–500 чоловік по заводу. На теперішній час все це робиться в системі і отримати можливо тільки те, що дозволено", — відмітив в своєму виступу Олександр Мінін, заступник директора по ІТ, Керівник проекту.
Система дозволяє прогнозувати неліквіди на 1–2 роки вперед. Постійні затрати скоротились на 20–30%. Всі управлінські рішення приймаються в електронному вигляді.
Чому не йдуть західні системи безпосередньо в управлінні виробництвом на території СНД?
Олександр Мінін озвучив свою точку зору: "У нас, в відмінності від західних заводів, на одному й тому ж майданчику і виробляється, і ремонтується складна продукція. Це зовсім різні по управлінню проекти, по суті конкуруючі між собою. А західні системи налаштовані на те, що це відбувається на різних територіях, коли матеріальні потоки практично не пересікаються. Також наше універсальне устаткування дозволяє запускати виробництво по різним технічним процесам, в результаті виникає можливість більшої кількості перепланувань".

Узагальнюючи досвід замовників, В. Михайлов виділив основні труднощі при оптимізації управління виробництвом:
1. Неготовність до залучення в проект всіх суміжних служб/директорів.
2. "Зашореність" низового виробничого персоналу та орієнтація в своїй роботі на "виробничі автоматизмі": всі започаткування можуть "вмерти в цехах", оскільки люди працюють так, як їх навчили 20 років назад.
3) Переваження старих обмежень, які при виникненні комплексної системи управління виробництвом вже не існують.
4) Орієнтація кожної служби на рішення своїх локальних завдань, а не на завдання підприємства, коли постачальники закупають матеріали великими партіями тому що "дають знижки", виробники запускають великі партії для повної загрузки потужностей і т. д.
5) Невисока активність в виробничих проектах першого керівника підприємства для рішення питань "на стику" служб, а це є дуже важливим, так як основні питання виникають на стику директорів департаментів і необхідний" верховний арбітр".
6) Неадекватність КД та ТД реальному виробничому процесу та довгий проміжок часу досягнення актуальності КД та ТД.
Оптимізація управління виробництвом: що робити не можна?
1. Не можна вирішувати завдання управління виробництвом тільки на рівні виробничих служб — необхідно залучення в "виробничий проект" комерційних та економічних служб та, по можливості, власників бізнесу.
З досвіду впровадження:
– "Неодноразово на нашому власному досвіді ми впевнились в тому, що, незалежно від того, як сформулюються цілі, поки генеральний директор не починає дієву участь в такому складному проекті, як впровадження ERP-системи, поки директор по виробництву не загинає всіх в відому "позу зю" і не говорить: "Будем працювати тільки в системі і ніяк по-другому", то, які б спочатку цілі не ставились, отримати які небудь результати буде неможливо".
– "Коли змінились власники та побачили стрибки по собівартості (один місяць 40 тис. за автокран, інший 80 тис.), то вони спочатку навіть не могли зрозуміти, прибуткове підприємство в принципі чи ні. А виявилось, що всі затрати просто списували на автокрани, відправлені на склад готової продукції. Така ситуація по суті й стала приводом для початку проекту. Ціллю стала прозорість управління підприємством та досягнення, як кінцевого результату, прибутковості. Цілі були визначені власниками, і вони постійно приймали участь в цьому процесі".
2. Неможливо вирішувати локальні завдання планування — необхідно багаторівневе наскрізне ковзне ітераційне планування виробництва. Необхідно передивитись всю систему управління виробництвом, починаючи з перспективного планування до середньострокового, оперативного планування продажу, виробництва, закупок, затрат.
3. Неможна вирішувати задачі управління виробництвом без зміни системи мотивації цехового персоналу.
"Кожна людина — це активна система, у якої є свої цілі. Ці цілі частіше не співпадають з цілями виробництва, — відмітив В. Михайлов, — В цехах придумують все що завгодно, аби щось не робити". Але все стає на свої місця і проблеми зникають самі собою, коли змінюється система мотивації і людям починають платити не за вал, а за виконання плану.
Із досвіду впровадження:
– "У першу чергу — цей проект реінжинірингу. Основна проблема, з якою ми мали справу , це відношення робітників до інновацій: "А ми так робили, а ми так працювали все життя, а зараз чомусь маємо по другому працювати".
На форумі своїм досвідом впровадження системи IT- Enterprise поділились ДП НВКГ "Зоря-Маш проект" (Миколаїв, Україна), концерн "Високовольтний Союз" (Єкатеринбург), ВАТ "Стройдормаш" (Алапаєвськ, Свердловської обл.), ВАТ "Дрогобицький завод автомобільних кранів" (Україна), ДП "ВО Південний машинобудівний завод ім. А.М. Макарова" (Дніпропетровськ, Україна), ВАТ "Кременчугський колесний завод", (Україна), ВАТ "Львівський локомотиворемонтний завод" (Україна).
Організатори форуму зібрали самі актуальні питання учасників, і під час "круглого" столу на них відповіли доповідачі.
З чого починати машинобудівному підприємству? Якими повинні бути перші кроки по впровадженню ERP-системи?
Тут доповідачі розділили перед проектну підготовку та початок самого проекта.
До проекту:
– "У нас так вийшло, що до початка цих робіт не давали коштів на навчання. А вже через рік ми почали вчитися. Прийшло розуміння, що потрібно вивчати методику для того, щоб іти дальше. Потім, на другому році впровадження проекта, вже маючи робочу систему та виниклі питання, ми відправились дивитись досвід других підприємств.
– "До проекта мають бути обов’язково сформовані чітко цілі. Вони мають бути не «про повернення інвестицій", а розроблені по всім направленим діяльності. Команда повинна бути чітко організована. Люди всередині команди повинні мати однакові прагнення. Навіть, можливо, прийдеться когось звільнити, щоб не було внутрішніх суперечностей".
– "У топ-менеджера підприємства має бути сформована чітка позиція: "що проект може дати і що при цьому вимагається від топів". Зараз уже подібної ситуації нема, но 5–7 років назад ми мали бажання мати одну велику кнопку, при наведенні якої "робиться все добре". А це принципово не можливо. Також до проекту являється важливим ознайомитись з методичною літературою, якої досить багато".
– "Однозначно повинно бути формування цілей та угода їх з інвестором. Тому що, коли проект вже іде, появляється дуже багато побічних завдань і бажань щось в рамках проекту зробити. Однак потрібно чітко розуміти, в що саме інвестор вкладає кошти, та двигатись за цим вектором".
– "1 етап: постановка цілей. 2 етап: формування команди. "Кадри рішають все" — це ключове висловлювання. Кадри як з сторони підприємства, так і з сторони команди впровадження. 3 етап: чітке формулювання ТЗ, і після цього розклад дії і безпосереднє виконання поставлених завдань.
Якщо говорити про довгострокові проекти, потрібно відмітити необхідність поєднання "низько" та "високо підвішених плодів". На перших етапах важливо рішить завдання для фінансистів, бухгалтерії".
Початок проекта:
– "Із свого досвіду: НДІ — це наше все. Побудова правильної системи нормативно-довідникової інформації — самий об’ємний етап по кількості труд затрат".
– "Перший етап (побудова НДІ, внесення даних) достатньо довгий та неприємний з точки зору протидії тих служб, які не розуміють, для чого це впровадження потрібно взагалі".
Як правильно ставити цілі по проекту впровадження?
– "Один із способів скорочення циклу — підйом ефективності виробництва. І багато що залежить від власника, від тих, хто ставить ціли. У нас, наприклад, підприємство державне, і наша ціль не порушити соціальну рівновагу у 12 тис. працюючих та дати гарантії тим, кого завод кормить у місті. І якщо скоротити цикл виробництва на 50% — для рівномірної загрузки потрібно скоротити ще понад 4 тис. робітників. Це неможливо по ряду причин, і така ціль не ставиться".
– "Якщо ціль, поставлена генеральним директором або власником підприємства, зафіксована за допомогою вивіреного в часі та кількості показників, то команда проекту повинна задатися питанням, а як ми впливаємо на досягнення цих показників, роблячи певний шаг у проекті".
Як бути якщо технологи не встигають описувати технічні процеси які вимагають? А встигають описувати тільки 10-15% — тільки самі складні деталі?
– "У нас 1200 чоловік на дослідному виробництві: 600 конструкторів, 400–500 технологів (цеховий та централізований відділи). Вони займаються як масовими змінами, так і розробкою нової техніки. У конструкторів багато систем (CAD,CAM), у технологів менше — но зараз іде масовий перехід на CAE системи, і за цим майбутнє".
– "Швидкість розробки технічних процесів, по нашому досвіду, після переходу на систему мінімум раз в п’ять перевищує те, що було раніше. Раніше технологів неможливо було примусити сісти за комп’ютер —вони писали на якихось папірцях, які потім передавались до цеху і часто губились. А тепер , після того як вони всі опанували комп’ютери , їх вже неможливо примусити писати на папірцях. Також часто технічні процеси у нас створюються на базі аналогів".
– "У нас близько 30 конструкторів та технологів, технологи є ще в цехах. У конструкторів у задачах — внесення змін і розробка нової техніки. Був період початкового вводу інформації— це дуже великий пласт роботи. Но тепер технологи мають встигати, інакше працювати не будуть. Якщо є той "доцент" на заводі, хто "заставить" — то всі технологи все встигають.
– "У нас встигають за рахунок дуже хорошої автоматизації. Плюс чітко налагоджена система. Любий технічний процес появляється з затримкою від конструкторського на два-три дні. Також активно використовуються комплекси лазерної різки, лазерної штамповки. На частину ДСЄ технологічні процеси формуються автоматично по певним заготовкам. Якщо поставлене завдання, то все виходить: технологічні служби здатні на багато".
– "Таке питання часто задають на початкових стадіях проекту. Це або проблема першого етапу, коли потрібно ввести дуже великий об’єм інформації (наповнення бази даних може зайняти біля півріччя), або це проблема того, що на заводі відсутній "доцент, який заставить". Через рік проблема "ми не встигаємо" іде сама собою".
Яка ступінь деталізації фактичної собівартості потрібна машинобудівним підприємствам?
Більшість підприємств на сьогоднішній день не бачать реальної фактичної собівартості хоча б з якоюсь зазначеною оперативністю. І до впровадження проекту вони не вважають, що це реально можливо.
– "Це питання індивідуальне для кожного підприємства. На нашому підприємстві необхідний максимально детальний облік, до кожної деталі, и ці вимоги економістів ставились перед початком проекту. Точність у визначенні собівартості збільшилась по мірі реалізації етапів проекту".
– "Якщо брати саме одиничне або малосерійне машинобудування, то для реального контролю собівартості необхідна деталізація та облік витрат до деталей та операцій по калькуляційним статтям по прямим витратам. Всі нинішні проекти ставлять такі цілі просто як даність: облік витрат та калькуляція до місця зберігання, переміщення витрат разом з деталлю в процесі переміщення між дільницями та цехами, списання витрат на зборку, накопичення на зборках та доведення до обліку готової продукції по кожному замовленню по фактичній собівартості і калькуляційним статтям. У 2012 році — це абсолютно реальна ціль".
– "Головна ціль обліку собівартості: фінансисти озвучують про наявність тендерів і необхідність розуміти, на який рівень ми можемо опуститися по зниженню ціни. І другий аспект — облік того, в якій точці починаються відхилення. Якщо на кінцевій точці ми зафіксували випуск виробу з собівартості вище або нижче планової — потрібно знати, де починаються данні відхилення.
З точки зору підприємства з довгим циклом виготовлення продукції: стадія підрахунків у нас починається у момент підготовки маркетингової служби до заключення договорів. Важливо розуміти, у що нам обійдеться цей виріб, для визначення правильної ціни. Складність закладена у коефіцієнтах росту ціни на матеріали. І тут вже багато в чому проявляється хист тих людей, які ведуть підрахунки. Система має механізми та формує всі данні, но необхідна людина, яка дуже тонко все відчуває. Експертів на промислових підприємствах дуже мало, наприклад, щоб правильно робити закупівлю металу, особливо за кордоном.
Необхідно відслідковувати відхилення та визначати, що на них впливає. Для визначення ефективності виробництва, важливо знати, при якій ціні ми отримаємо прибуток і скільки буде стояти точно також вироби при запуску у виробництво".
– "Більшість підприємств більше за все цікавить оперативність фактичної собівартості: "бачити сьогодні, максимум учора, скільки в наших замовленнях лежить фактичної собівартості ". Відхилення стають критичні, коли, наприклад , на 70% готове замовлення з продажною ціною в 1 мільйон., но фактичною собівартості в ньому вже 900 тис. Потрібно бачити, де і в чому відхилення, та приймати відповідні рішення".
– "Прибуток не є основним показником. Важлива ще маржинальна складова. Є механізм, но якщо нема людей, які уміють працювати з ціною, то не завжди буде потрібний ефект. І навчання персоналу — дуже важлива річ. Ціль оперативності — у момент відхилення факту від плану це повинен побачити керівник і швидко прийняти організаційні рішення".
Як вирішується питання, зв’язане з управлінням змінами?
– "Проблема з цим дуже велика, зараз вона стала менша, но ще існує і зв’язана з ефективністю. Всім видно, коли з’являються зміни. Впроваджується новий технічний процес, проходять зміни закупочного матеріалу, і технолог говорить: що цей процес впроваджений, планування повинно проходить по новому технічного процесу з другими матеріалами.
Но, на приклад, на складі зависло 1,5–2 т металу. Встає питання: в який момент потрібно починати працювати по новому технічного процесу ? Видно, потрібно спочатку цей метал витратити, бо в нього вже вкладені кошти. Також потрібний час на закупівлю нового матеріалу.
Зараз у нас, із-за того що люди часто і швидко бачать зміни які проводяться, почалась взаємодія між службами по визначенню моменту вводу змін.
В цілому, в процесі впровадження системи питання змінюються. Зміни у нас вже проходять по всьому ланцюжку, но стоїть питання по ефективності і часу проведення цих змін. І ми зараз якраз на цій стадії — як добитися ефективних змін завчасно".
– "Ефективні зміни — це велике питання, однозначної відповіді на який дати тяжко. Є ще один нюанс — коли відбуваються любі зміни и ми розуміємо, що є визначене питання, зв’язаний з незавершеним виробництвом, то потрібно вирішувати: що робити? Як врахувати цей об’єм незавершеного виробництва, як його повернути назад на виробництво, точки зору його придатності у змінені продукції. Це питання присутнє, и ми його поки рішаємо організаційно на рівні описаних процедур".
– "Питання, особливо, болюче для всього машинобудування. Зараз майже у всіх це персоналізація виробу. Саме життя заводу — це і є вал змін, який повинен коректно доходити до точки, де іде обробка металу, виготовлення деталей і т. д.
тому направлень декілька.
Перше — це персоналізовані склади та технічні процеси на заказ, що повинна дозволяти робити ІС. Якщо MRP-план видається за мінусом незавершеного виробництва, то по стану цього плану вже можливо зрівнювати ці зміни з присвоєним номером заказу і т. д.
Друге — це система досягнення цілей, коли є документ і потрібно все це коректно відпрацьовувати. Без інформаційної системи, коли ці зміни ідуть наскрізним шляхом, я просто не уявляю, як це можливо робити".
– "У нас, на жаль, інструмент відсутній, но окреме управління змінами є у технічної документації. Коли у 2005–2007 рр. основні цілі проекту були досягнуті і сформована програма розвитку, почалася криза. Тоді зупинилось фінансування впровадження управління змінами у системі. І так як ми не володіємо даним інструментом, то залишаються тільки організаційні методи".
– "Якщо говорити про технічні механізми, то їх має бути декілька, починаючи з оповіщення: головний технолог кожний день в ранці бачить, які з’явились нові конструкторські документи, по яким відстає технологічний департамент.
У нас також є на цей момент проблема, коли конструктори випускають сповіщення на зміни, а в цей момент три або чотири замовлення виконуються по попередній версії документації. Причому вже половина ДСЄ зроблена по старій документації, а друга навіть не починалась робитися — цю проблему рішаємо; думаю, найдем якісь технічні варіанти. Я не бачу особливо принципової складності в цьому питанні — це проблема, яку потрібно рішати.
Ситуація наступна: є до 80 тис. ДСЄ, які входять у замовлення, і при цьому міняється одна вибрана позиція тільки для даного конкретного заказу. Є спец інструмент у системі — попередні сповіщення, які в електронному вигляді з мінімальним циклом домовляються у системі і дальше, в момент затвердження по нажатої одної кнопки, вони зразу доводяться до виробництва. В цей же день перераховується MRP-план, і на наступний день, з ранку, всі завдання, які отримує виробництво, вже враховують всі ці зміни".
– "Крім загальноприйнятих попередніх сповіщень, у нас є планові та аварійні питання. Аварійні — це вихід техніки із строю, і сповіщення направлені на усунення помилок, а також захід, який дозволяє знижувати витрати, і відповідні сповіщення.
Ми ліквідували практично весь ланцюжок домовленостей, коли я, як заступник головного технолога, підписував один документ с грифом "Т" (терміново), і на наступний день ці зміни вже були у виробництві. То це є чисто організаційний момент. Після впровадження це почали проводити у самій системі".
За відгуками учасників заходу, подібний обмін думками, вивчення досвіду по рішенню самих різних питань і проблем з колегами виявились дуже корисними. Як учасники, так і Портал машинобудування мають надію, що Форум буде проводитися щорічно.
А так як Форум проходив недалеко від Одеси, то неформально поспілкуватися учасники змогли під час екскурсії по місту, відвідування театру та дегустації вина на старовинному виноробному підприємстві "Французький бульвар" .
Див. також
Звітний відеоролик про роботу Машинобудівного форуму 2012
ВСІ ПРОЕКТИ ВПРОВАДЖЕННЯ СИСТЕМИ IT-ENTERPRISE НА МАШИНОБУДІВНИХ ПІДПИЄМСТВАХ